As one of the earliest pioneering Hand Pan Builders, we have explored a LOT of ways to build these instruments.
We have spent years exploring different note shapes and sizes, border designs, dimple shapes, dimple to note ratios, port and interstitial designs, note alignments, bottom notes, helmholtz tuning, fine shaping methods, hammered, drawn, and hydro-formed shells, cold rolled steel and stainless steel. We are always exploring further developments as this young art form continues to grow. We are delighted to offer the sum of many tens of thousands of hours of development in the current chapter of our creative skills.
The following are some behind the scenes photos of our development and building process. Thanks so much for your interest in the Saraz.
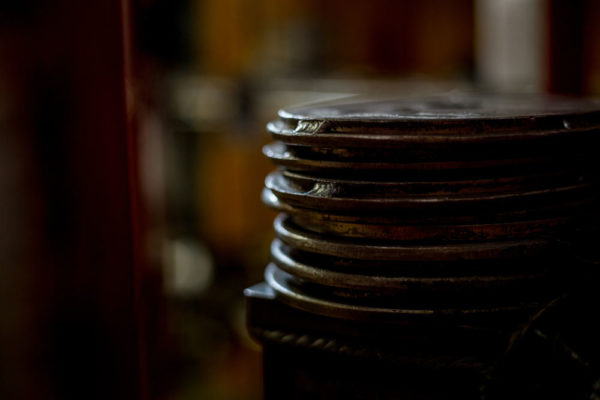
We have a different steel form for each note, currently from F#2 – C#6 and still expanding in both directions.
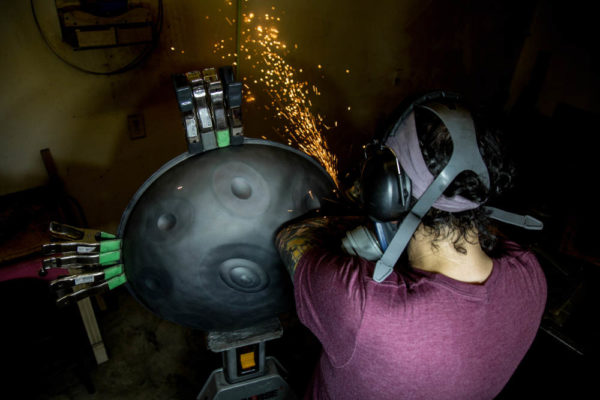
We grind a lot of rims!
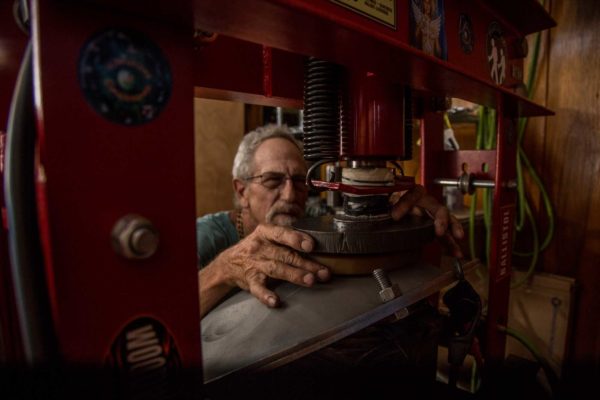
We simultaneously press most dimples and tone fields. The pressure necessary exceeds 40 tons for the biggest notes. While the press makes a uniform dimple and tone field, there is still hours of pneumatic hammering to do afterward on the interstitial areas.
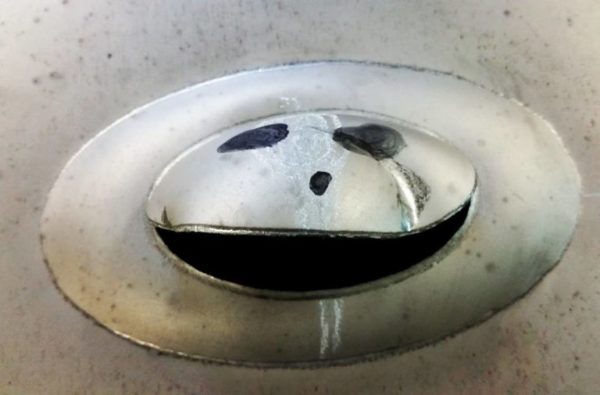
It doesn’t always go perfectly
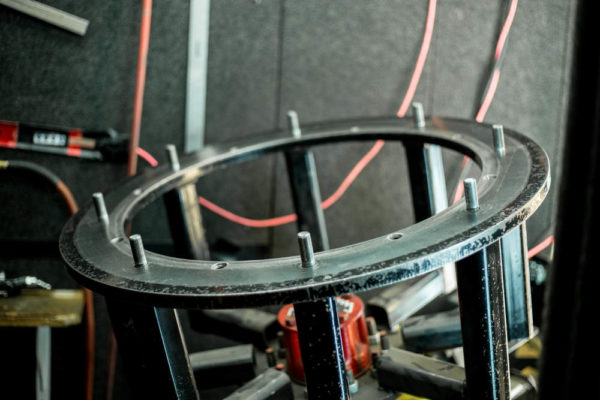
This is “Big Mo”, a motorized sinking and shaping table designed and built by the late Jim Dusin of Pantheon Steel. The inner diameter is a bit more than 21″. We also have rings with 19″ and 20″ inner diameter for creating the 3 sizes of Saraz.
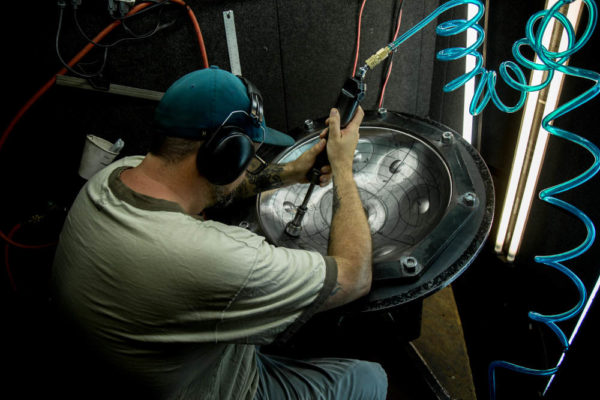
We estimate that each fully hammer shaped Saraz is hit over 200,000 times.
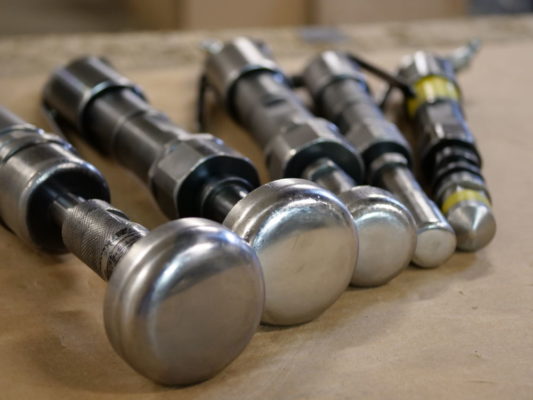
These are the modified pneumatic sand rammers that we use for sinking shells and all fine shaping.
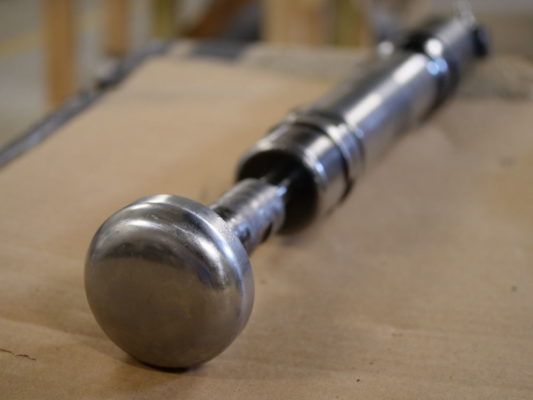
Our largest pnuematic hammer and head. We use this for 95% of the shell sinking process.
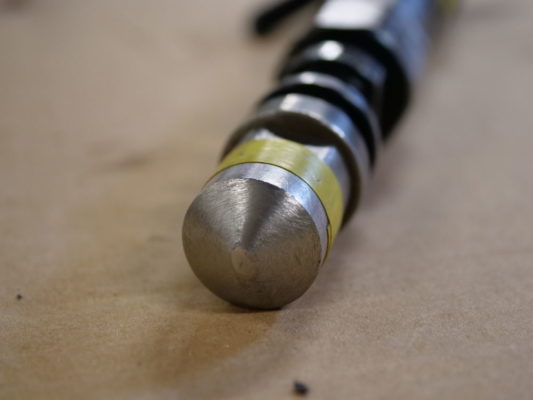
Originally fabricated by Pantheon Steel, we have altered this head many times for shaping the finest details in the interstial around notes, the rim and to create border tension.
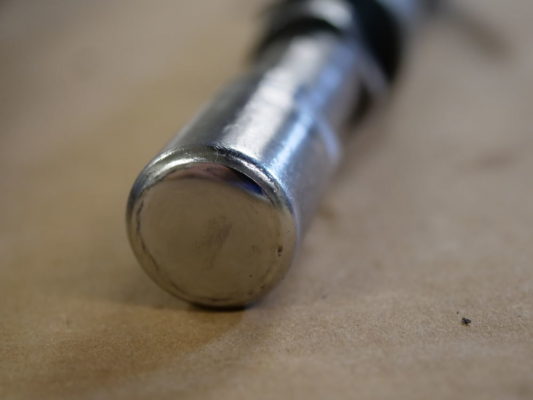
We use this hammer head for general fine shaping in the interstitial as well building note borders.
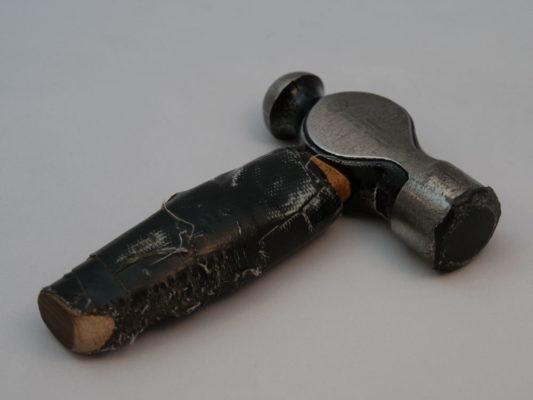
The “third thumb”. This 16 ounce $5 hammer was altered to be our main tuning hammer. We use it for approximately 80-85% of the tuning process.
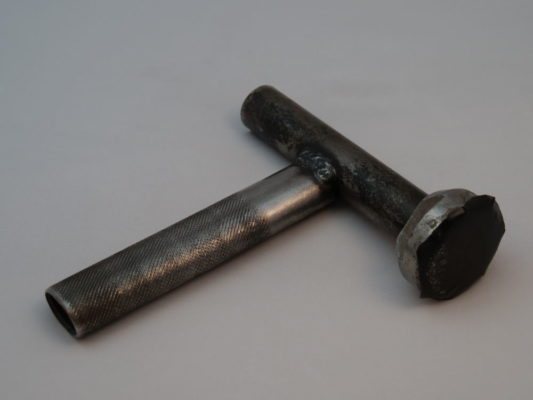
Fabricated by Pantheon Steel, this 2 pound hammer is used mostly for loosening notes.
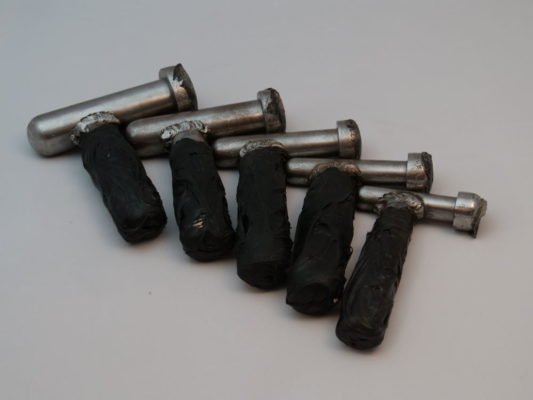
These 5 hammers were fabricated by Rhythmical Steel primarily for tuning Steel pans. We use the #1 for increasing amplitude of high harmonics, #2 and #3 for decompressing interstitial areas, #4 and #5 for tuning ports and for reshaping interstitial during handpan repairs.
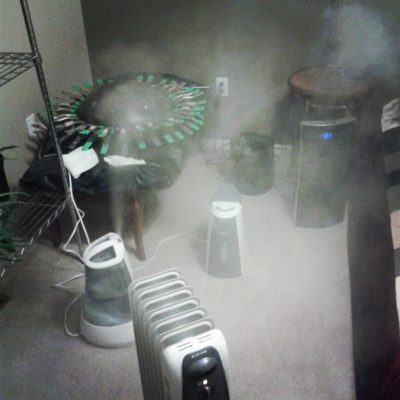
The glue that we use is part of the magic of the timbre. It is particularly important to follow the directions and use it above 70 degrees F and 50% humidity. During the Asheville winter, this requires a heater and at least one humidifier.
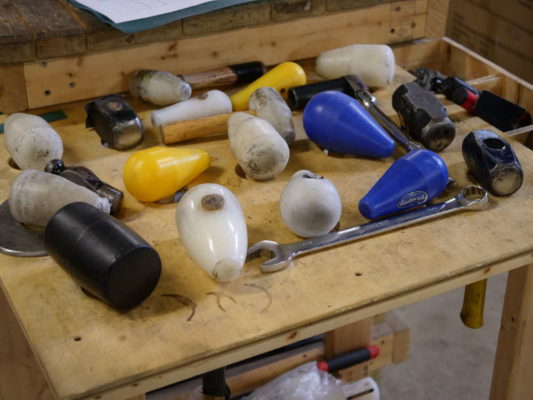
For our highest notes and for forming ports, we use bossing mallets and a sledge hammer.
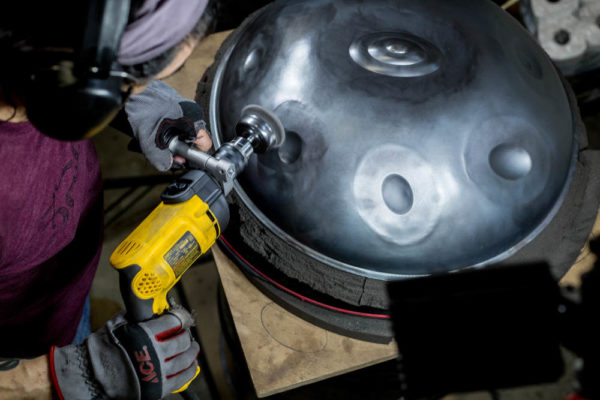
We polish each Saraz with a steel cup brush on a drill. We find that smoothing the surface eliminates porous absorbent texture and increases rust resistance.
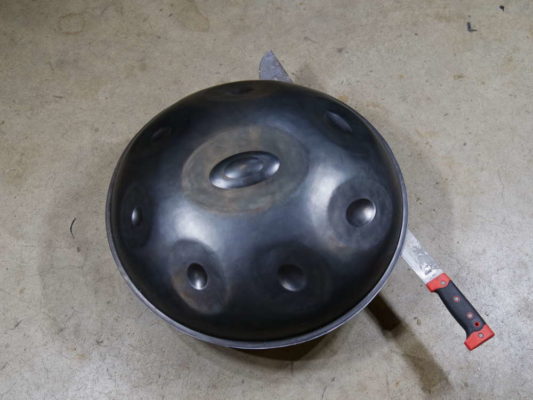
We occasionally need to cut instruments open during handpan repairs or if the glue does not cure correctly. While we have been working on our single swing Samurai chop, we mostly take it much more slowly by first penetrating the glue with a knife and sledge hammer and then hammering on the back of a machete until we get through all of the cured glue.
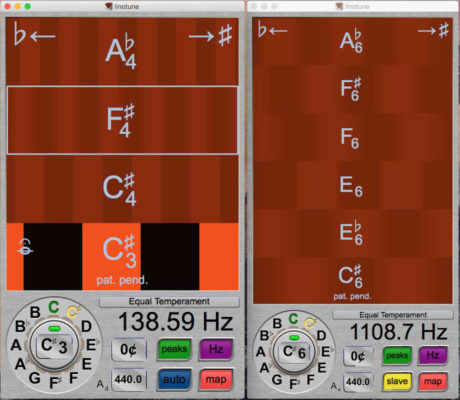
We use Linotune software primarily for our tuning needs. It is an incredibly powerful program designed for fine tuning. When tuning ports and shoulder tones, we also use the GTune Software spectra graph to look at all present frequencies while using linotune to fine tune.
Want to learn more about how we build the Saraz?
Please visit our Handpan Construction Pages.
In Stock and Custom Order Handpans for sale
“Dear Saraz family, Thank you guys so much for this pan. This F dorian sound make me speechless. The tone is softly touching my soul and the vibration is dancing a Tango with my heart. The pan arrived in perfect condition, your service was great.”